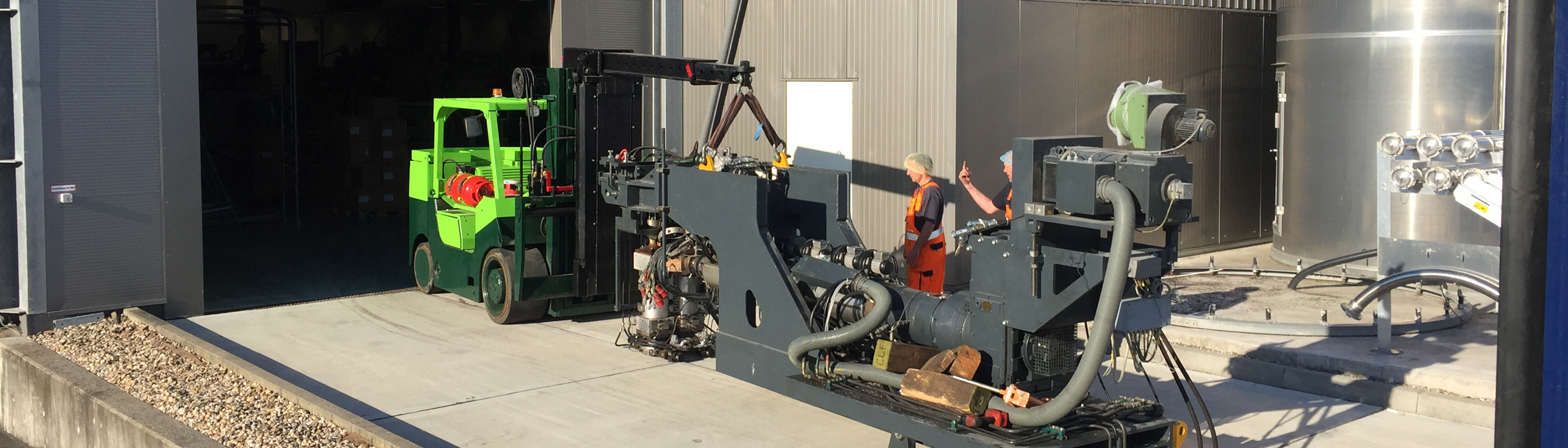
International Relocation
Scope:
To dismantle, load and relocate two oversized blow moulding production lines along with all ancillary components and spares. The production lines will need to be delivered to two separate UK sites so that they can be unloaded, positioned to a centre line and assembled within the new locations.
Difficulties:
When undertaking the disassembly of the machinery extra care must be taken to avoid the internal overhead services and service gantry. All conveyor track way and associated equipment would need to be dismantled and removed to allow access to the blow moulding machines. All HGV transport vehicles supplied had to meet the European legislation with regard to vehicle dimensions and weights. This meant that all HGV vehicles could not exceed 40,000kg and that no load could project outwards from the vehicle without an abnormal load permit. All equipment moved on transport had to be carefully restrained to meet European legislation. Any loads that would require to be sheeted must be covered in such a manner that it did not impede on the restraint of the load. The co ordination of multiple assets had to be tightly controlled so that the correct equipment or vehicle arrived to the agreed timetable.
All abnormal load permits had to be in place to suit the size of the load which must meet the given dimensions and weights to obtain the permits. Both production lines needed to be segregated and loaded into transport for delivery into the UK. A team within the UK would receive the goods and unload the items at the delivery destinations. They would need clear communication to understand exactly what was in transit and its expected arrival date/time.
Method:
All necessary equipment was loaded onto an artic and despatched to the German collection destination in preparation for the arrival of our personnel. This included one of our Versa-Lift’s and a mobile workshop containing our equipment and tools. Upon arrival to Germany all conveyor track way was match marked prior to disassembly and was prepared for loading into several curtain sided vehicles along with all associated equipment. The two blow moulding machines were also individually match marked prior to disassembly. This included all panelling, walkways and main machinery components. The two oversized blow moulding machines were stripped down to their absolute minimum to allow a safe onward movement. This involved the removal of the injector heads, hydraulic packs and press heads via the use of our Versa-Lift.
Once all components were removed from the machine they were loaded on to abnormal load transport and sheeted to protect the loads from any adverse weather whilst in transit. The heavier components of the machinery that were too heavy to lift with the Versa-Lift were placed on to skates and towed from within the facility in to a position that a mobile crane could lift them and place on to abnormal load transport. One of the two production lines was transported directly to one of clients UK facilities where it was unloaded and placed into the facility for storage. The second production line was delivered to our storage facility for a short period of time until the client was ready to accept the production line within a second UK based facility.
Once the client was prepared to accept the machinery within the manufacturing facility it was loaded up for transport, including all equipment required to undertake the install of the machinery and delivered to site. The machinery was unloaded, positioned to a centre line and assembled within the new facility to meet the client’s exact requirements using the same equipment that was supplied to dismantle it within the German facility.